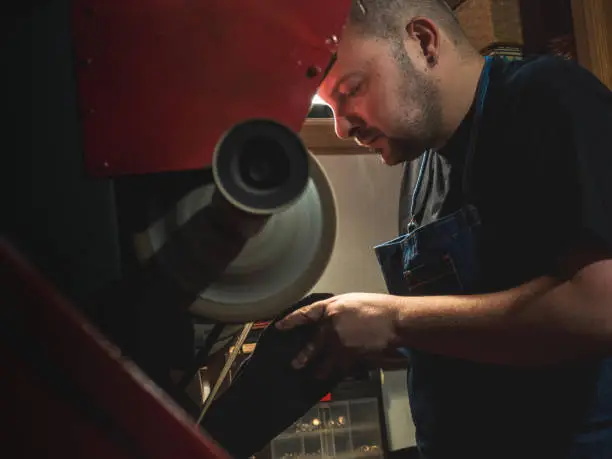
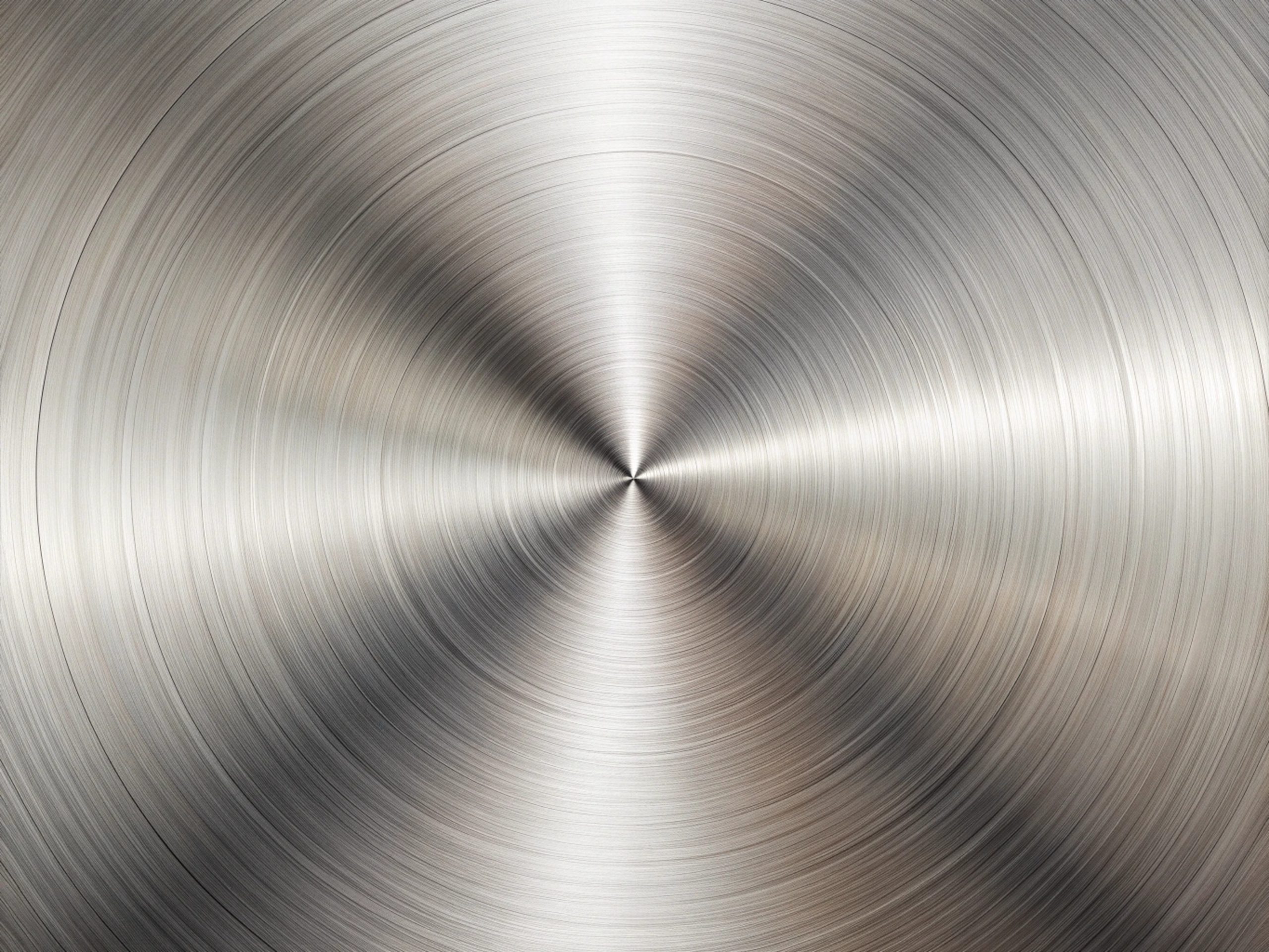
Why Metal Polishing is Essential After Metal Spinning
Metal spinning is a precise and efficient method for forming cylindrical and conical metal parts, widely used across industries such as aerospace, automotive, and manufacturing. The process involves rotating a metal disc or tube at high speed while shaping it using a tool. While metal spinning offers numerous benefits, including cost-effectiveness and material efficiency, the components produced often require additional finishing to enhance their performance, durability, and aesthetic appeal. Here, metal polishing becomes an essential step in the overall manufacturing process.
Enhancing Surface Quality and Aesthetic Appeal
One of the primary reasons for metal polishing after metal spinning is to improve the surface quality of the metal. Though highly efficient, metal spinning can leave behind tool marks, minor imperfections, and a slightly rough texture. Polishing smooths out these inconsistencies, creating a refined and uniform surface that is visually appealing and super smooth.
In industries where appearance is critical—such as automotive design, luxury goods, and interior architecture—metal polishing ensures that products meet the highest aesthetic standards. A polished metal surface reflects light uniformly, giving a premium look that is often a requirement for high-end products. Whether used for a gleaming automotive component or a decorative architectural feature, polished metal enhances both function and form.
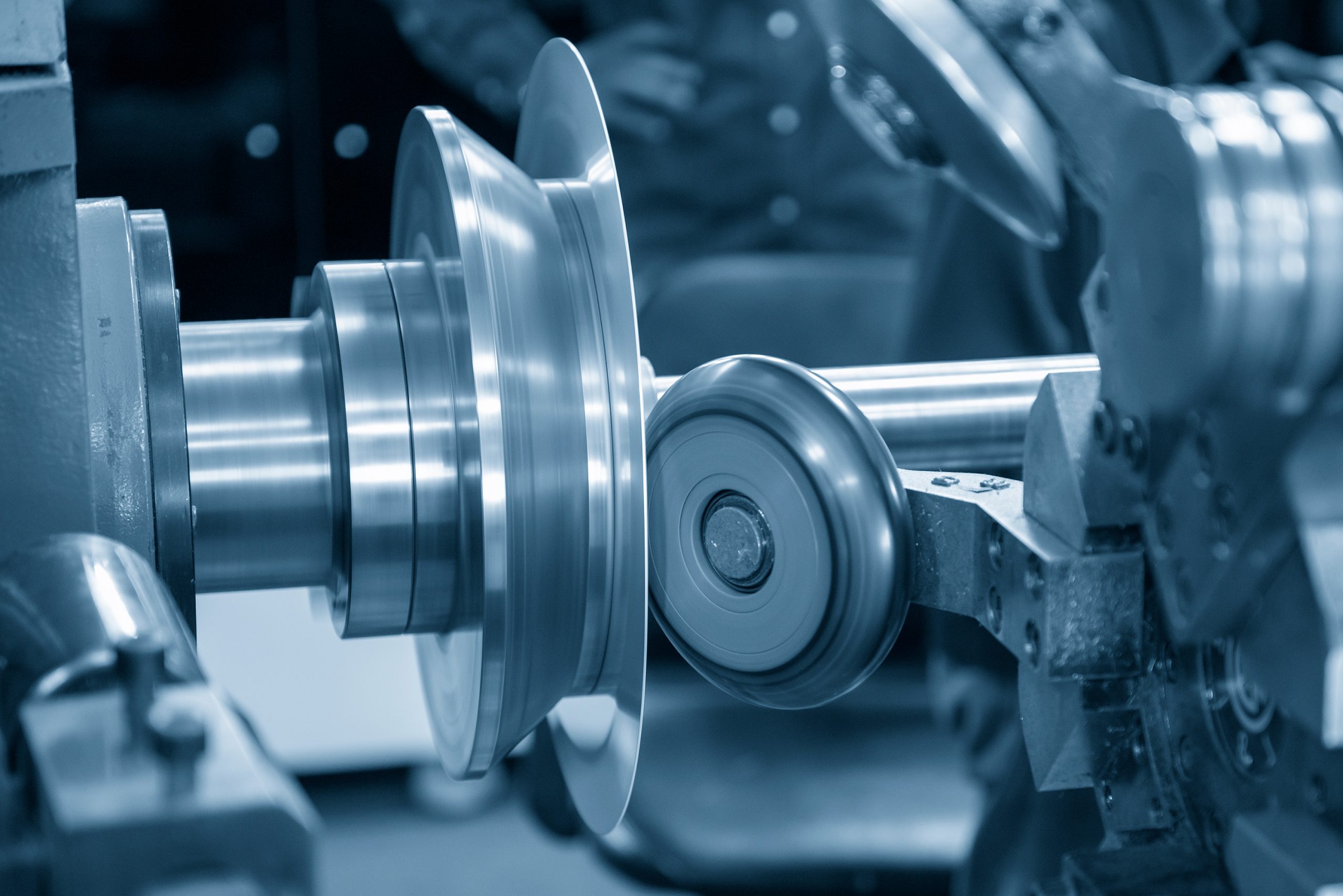
Improving Corrosion Resistance
Metals often work in harsh environmental conditions, with moisture, chemicals, and extreme temperatures contributing to corrosion over time. Unpolished metal surfaces can have microscopic crevices where contaminants and moisture accumulate, accelerating the corrosion process. Polishing eliminates these irregularities, reducing the risk of oxidation and subsequent corrosion and increasing the component’s lifespan.
Polishing is often used in conjunction with other protective coatings or treatments, such as anodizing, plating, or passivation. These additives adhere more effectively to a polished surface, so the combination further enhances corrosion resistance in metals. This application is particularly important in industries such as marine engineering, medical device manufacturing, and food processing, where metal components must maintain integrity over prolonged periods of use.
Enhancing Mechanical Performance and Wear Resistance
Beyond aesthetics and corrosion resistance, metal polishing also improves the mechanical performance of spun metal components. Surface roughness can lead to increased friction when parts come into contact with each other, which increases wear and tear over time. Polishing significantly reduces friction by smoothing the surface, offering improved wear resistance and longer-lasting components.
For moving parts such as bearings, gears, and turbine components, a polished surface reduces energy loss caused by friction. This change contributes to greater efficiency and longevity, particularly in high-performance machinery where durability is a key concern. In applications where precision is critical, such as aerospace and medical industries, polished metal ensures long-term consistency and reliability.
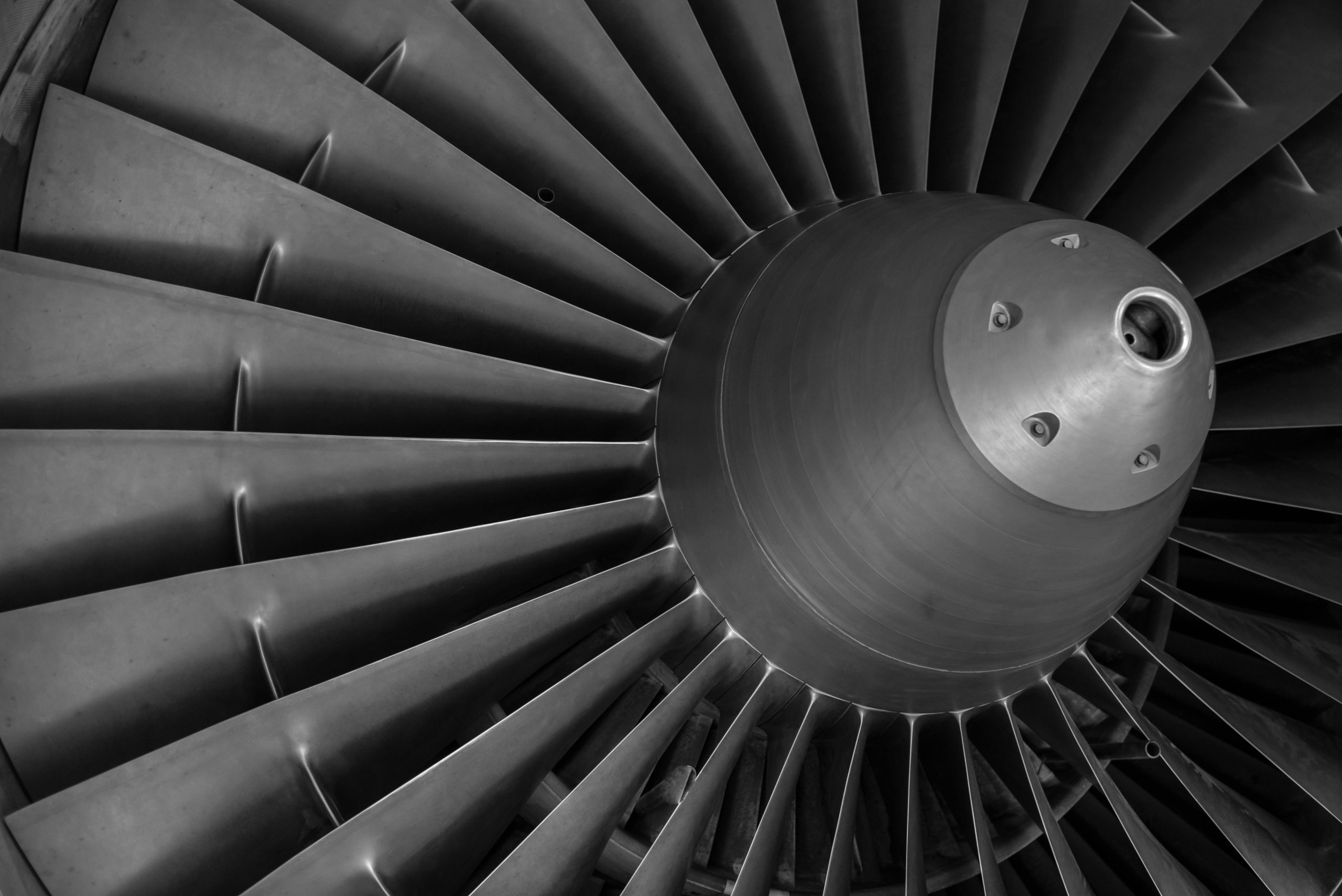
Facilitating Coating and Plating Processes
For metal components that undergo additional finishing processes such as powder coating, electroplating, or anodizing, polishing creates an ideal surface for these coatings to bond effectively.
For instance, in the automotive industry, many components are chrome-plated or powder-coated to provide additional protection and aesthetic appeal. If the underlying surface is not correctly polished, defects in the metal can become apparent once the coating is applied, leading to rework and increased production costs. Proper polishing ensures that the final product meets the highest standards of quality and durability.
Removing Oxides and Contaminants
Heat and mechanical stress can also cause oxidation and contamination on the metal surface during the metal spinning process. These unwanted residues can weaken the metal, reduce conductivity in electrical applications, and compromise hygiene in food and medical industries. Metal polishing removes these oxides and contaminants, restoring the metal to optimal condition.
For example, in the electronics industry, polished metal components deliver better conductivity and offer more reliable performance in sensitive equipment.
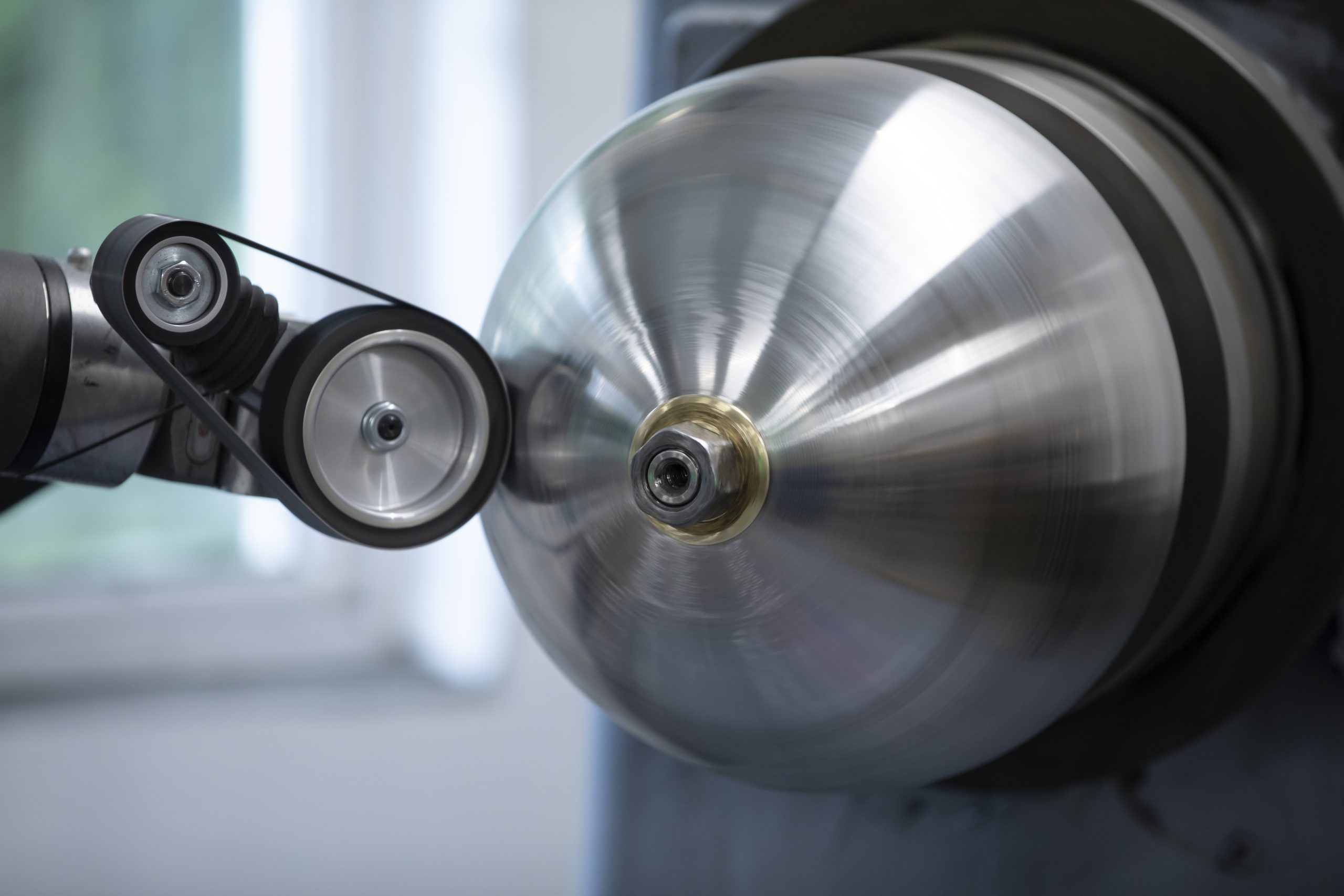
Meeting Industry Standards and Compliance Requirements
Various industries impose strict quality and safety standards that dictate the required surface finish for metal components. Medical, food processing, and aerospace sectors, in particular, have stringent regulations regarding metal cleanliness and smoothness. Polishing is often necessary to comply with these standards and ensure that products meet safety and performance criteria.
In the food industry, stainless steel equipment used in processing and packaging must be polished to a specific level to prevent bacterial growth and facilitate easy cleaning. A rough or porous surface can trap food particles and lead to contamination risks. Similarly, in aerospace applications, polished metal surfaces reduce the risk of stress fractures and fatigue, ensuring the structural integrity of critical components.
Increasing the Lifespan of Metal Components
By reducing roughness, eliminating stress points, and enhancing corrosion resistance, polished metals are better equipped to withstand mechanical and environmental stressors. Investing in metal polishing after the spinning process significantly extends the lifespan of metal components. This enhancement translates to lower maintenance costs, fewer replacements, and improved overall efficiency in industrial applications.
For polished metal parts in high-stress environments, such as turbines or engine components, this improvement contributes to better performance, reduced downtime, and significant cost savings for manufacturers and end-users alike. The initial investment in polishing pays off in the long run by improving durability and reliability.
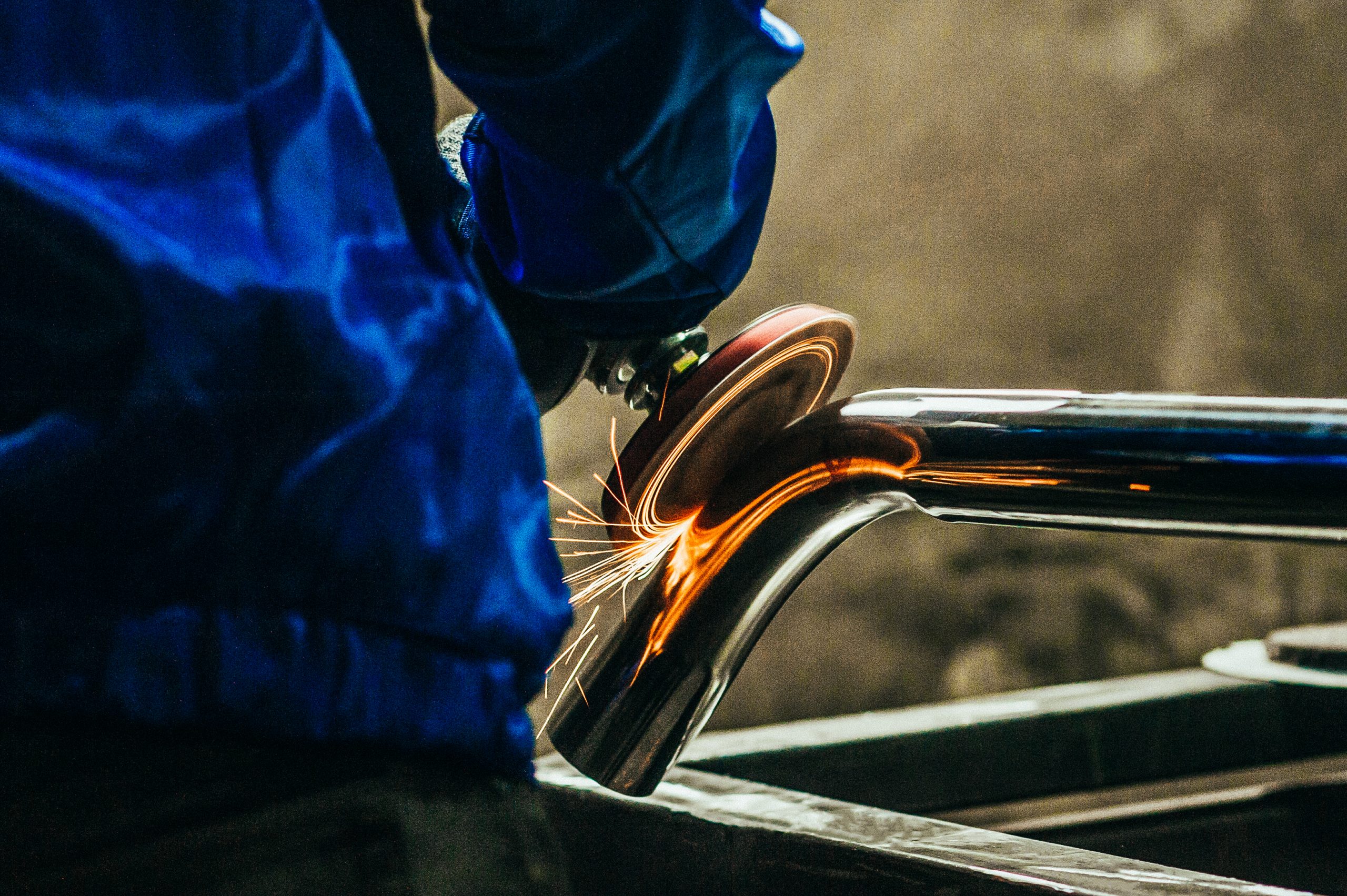
Achieving Excellence Through Metal Polishing
Metal polishing is not merely an aesthetic enhancement—it is a critical process that significantly improves the quality, performance, and longevity of metal-spun components. From enhancing corrosion resistance and mechanical performance to facilitating coating adhesion and meeting industry standards, polishing is an indispensable step in ensuring superior product quality.
Whether for aerospace, automotive, medical, or industrial applications, polished metal components stand the test of time, delivering optimal performance and unmatched reliability.
By understanding the essential role of metal polishing after spinning, manufacturers can make informed decisions that enhance the value and efficiency of their metal products. Investing in precision polishing ensures that every spun metal component achieves its full potential, delivering lasting benefits across a wide range of industries.
At Tanfield Metal Spinners, our commitment to excellence extends beyond metal spinning. By incorporating advanced polishing techniques, we ensure that every component meets the highest durability, functionality, and visual appeal standards.
Contact Us Today!
We encourage you to reach out to us today, our team of knowledgeable experts is ready to answer your questions, provide personalised guidance, and help you find the right solution for your needs.
Contact Us